Common Welding Repair Work Issues and Just How to Address Them Efficiently
Welding repairs commonly encounter a variety of issues that can threaten the integrity of the last item. Usual problems consist of insufficient penetration, porosity, and imbalance, to name a few. Each defect provides unique difficulties that require specific strategies for resolution. Recognizing these issues is vital for welders intending to improve their end results and skills. This conversation will certainly explore these typical welding repair problems and efficient techniques to address them.
Poor Penetration
Inadequate infiltration occurs when the weld steel stops working to fully fuse with the base product, resulting in weak joints and possible structural failures. This concern typically originates from insufficient heat input, wrong electrode angle, or incorrect welding speed. Welders may run into poor penetration due to a miscalculation of the required criteria for a specific material thickness or type. Additionally, contamination on the base product's surface area can hinder effective bonding, exacerbating the trouble. To address poor penetration, welders ought to assure appropriate settings on their devices and keep a clean work surface. Normal examination of welds is advised to identify any type of deficiencies early, permitting prompt corrections and the prevention of endangered structural stability in bonded assemblies.
Porosity
Porosity is a typical problem in bonded joints that manifests as tiny gas bubbles caught within the weld steel. This flaw can endanger the integrity of the weld, causing lowered stamina and possible failure under anxiety. Montana Mobile Welding and Repair Belgrade Fabrication. Porosity typically occurs from contamination, moisture, or inappropriate welding techniques, which permit gases to run away right into the liquified weld swimming pool. To resolve porosity, welders ought to ensure correct surface preparation, preserve a tidy workplace, and utilize ideal welding parameters. In addition, selecting the ideal filler material and protecting gas can minimize gas entrapment. Routine assessment and testing of welds can aid identify porosity early, guaranteeing timely corrective activities are taken, thus protecting the top quality and dependability of the welded structure
Imbalance
Misalignment in welding can emerge from numerous variables, including incorrect setup and thermal expansion. Understanding the source is necessary for efficient resolution. Numerous modification techniques are offered to realign parts and assure structural honesty.
Reasons for Misalignment
Welding imbalance commonly stems from a selection of underlying issues that can endanger architectural integrity. One key reason is incorrect fit-up of parts prior to welding, which can lead to voids and unequal surfaces. Variations in thermal growth during the welding process can additionally lead to distortion, especially if the products being signed up with have different coefficients of expansion. Additionally, poor fixturing and securing might stop working to hold components safely in area, causing movement during welding. Badly conserved equipment, consisting of welding machines and tools, may present inconsistencies in the weld grain, more adding to misalignment. Finally, driver error, originating from inadequate training or experience, can additionally play a significant role in producing misaligned welds.
Modification Methods Available
Resolving misalignment efficiently calls for a combination of restorative strategies tailored to the certain problems handy. One usual approach is the use of jigs or components to hold elements in the correct setting throughout welding, making certain regular positioning. Additionally, preheating the materials can help in reducing distortion and boost fit-up. For substantial misalignment, mechanical adjustment strategies, such as making use of hydraulic jacks or clamps, can be utilized to deal with the position prior to welding. Post-weld warmth treatment might likewise be needed to ease tensions caused by misalignment. Lastly, mindful evaluation and adjustment during the arrangement stage can protect against imbalance issues from coming to be significant problems, advertising a smoother welding process and improving general architectural integrity.
Distortion
Distortion is a common obstacle in welding that can emerge from different elements, consisting of unequal heating and air conditioning. Recognizing the causes of distortion is crucial for applying efficient prevention techniques. Resolving this problem not just boosts architectural integrity yet additionally enhances the overall quality of the weld.
Causes of Distortion
When based on the intense warmth of welding, products commonly go through adjustments that can lead to distortion. This sensation primarily emerges from thermal development and tightening during the welding process. As the weld location warms up, the material increases; upon cooling, it gets, which can develop interior anxieties. Furthermore, unequal home heating across a workpiece can aggravate these anxieties, resulting in warping or bending. The kind of material likewise plays a considerable duty; metals with varying thermal conductivity and coefficients of development may respond in a different way, leading to uncertain distortions. Additionally, poor joint design and insufficient fixturing can add to imbalance throughout welding, increasing the probability of distortion. Comprehending these causes is important for efficient welding fixing and prevention techniques.
Avoidance Techniques
Reliable prevention strategies for distortion throughout welding concentrate on managing warmth input and making sure proper joint style. Keeping a constant heat input helps to decrease thermal expansion and tightening, which can bring about distortion. Making use of methods such as preheating the workpiece can also lower the temperature level slope, advertising consistent home heating. Furthermore, picking suitable joint layouts, such as T-joints or lap joints, can boost security and decrease anxiety concentrations. Implementing appropriate fixturing to safeguard the work surfaces in position additionally help in keeping alignment throughout the welding procedure. Staggered welding series can disperse warm extra evenly, avoiding localized distortion. By applying these approaches, welders can substantially reduce the likelihood of distortion and boost the total top quality of their welds.
Cracking
Breaking is an usual problem come across in welding fixings, often arising from different variables such as incorrect cooling rates, material option, or inadequate joint preparation. The incident of fractures can substantially compromise the integrity of the weld, bring about prospective failings during operation. To address this problem, welders should initially examine the root causes, making sure that materials useful link are suitable and appropriately selected for the particular application. In addition, regulating the cooling price throughout the welding procedure is vital; quick air conditioning can generate tension and bring about cracking. Proper joint layout and preparation likewise add to reducing the risk. Executing these approaches can enhance weld high quality and sturdiness, inevitably decreasing the likelihood of fracturing in completed weldments.
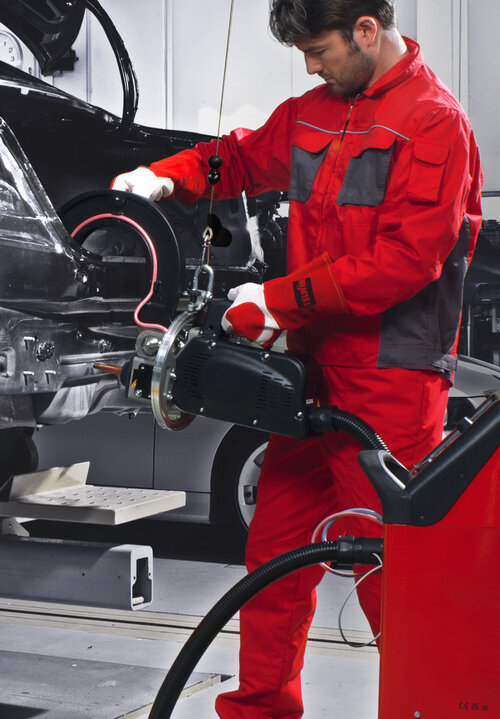
Incomplete Blend
A considerable concern in welding repair work is insufficient combination, which occurs when the weld metal does not effectively bond with the base product or previous weld passes - Fabrication. This problem can lead to weak points in the joint, possibly compromising the stability of the welded structure. Variables contributing to incomplete combination include insufficient heat input, inappropriate welding method, and contamination of the surface areas being signed up with. To address this concern effectively, welders ought to guarantee proper pre-weld cleansing and surface preparation, along with readjust their welding parameters to attain adequate penetration and combination. Routine evaluation throughout the welding procedure can additionally help recognize insufficient fusion early, permitting timely corrective actions to improve the overall quality of the weld
Overheating
While welding repair services can improve architectural integrity, overheating offers a significant challenge that can bring about material destruction. Extreme heat during welding can modify the mechanical residential or commercial properties of steels, causing reduced toughness, raised brittleness, and warping. This phenomenon is specifically vital in high-stress applications where architectural reliability is critical. Recognizing getting too hot can entail go to website visual evaluations for discoloration or distortion, along with monitoring temperature level throughout the welding process. To reduce the dangers associated with getting too hot, welders ought to employ proper strategies, such as managing warmth input, readjusting traveling rate, and utilizing appropriate filler materials. In addition, implementing pre- and post-weld heat therapies can aid recover material residential properties and improve the overall high quality of the repair work, making sure long-term efficiency and security.
Frequently Asked Questions
What Are the Usual Indications of a Welding Flaw?
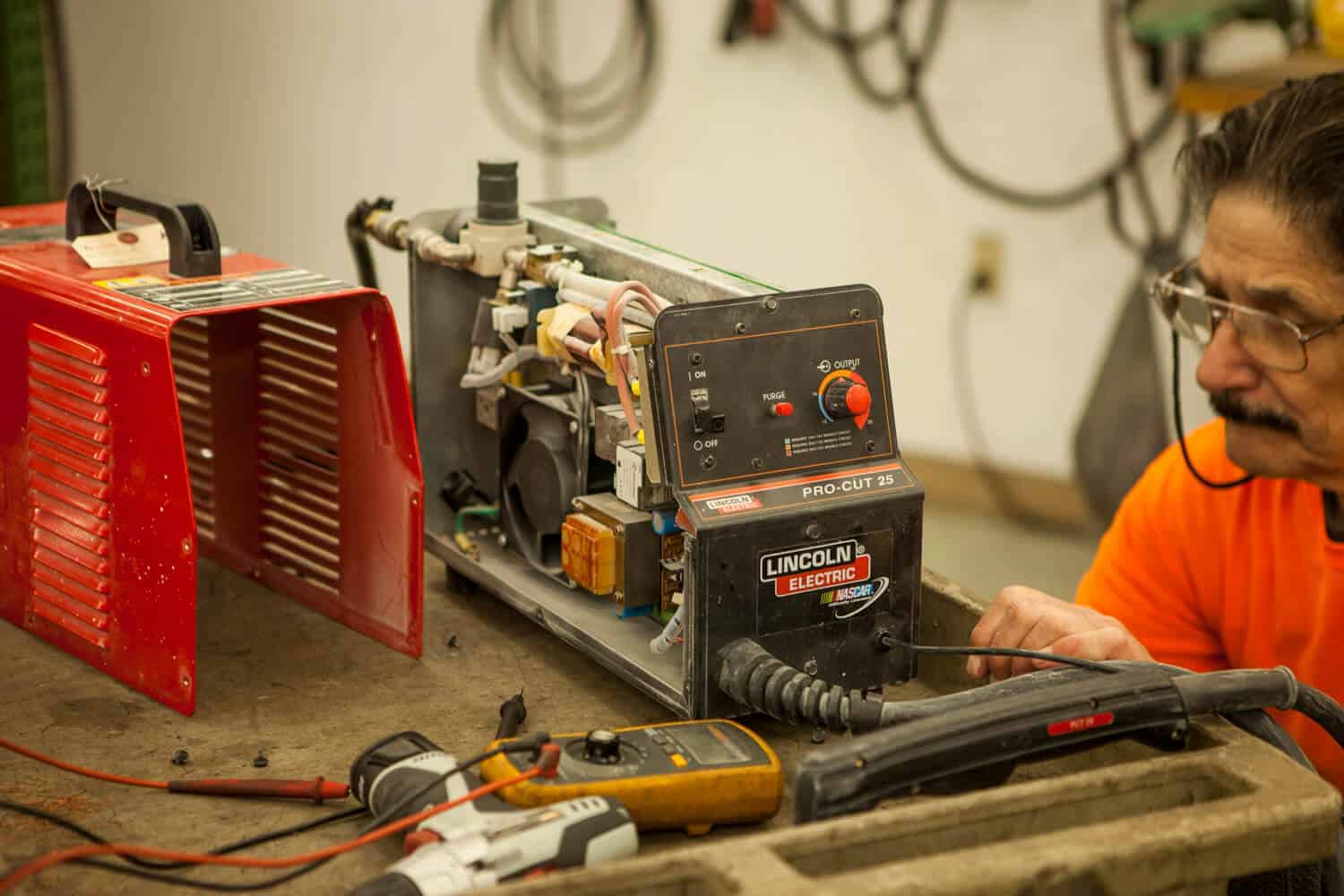
Exactly How Can I Test My Welds for High quality?
To evaluate welds for top quality, one can utilize aesthetic inspections, ultrasonic testing, and radiographic methods. Each technique guarantees structural stability, determines flaws, and confirms adherence to specified requirements, inevitably enhancing the reliability of the bonded joints.
What Safety Preventative Measures Should I Take While Welding?
When welding, one need to focus on safety by putting on proper personal safety equipment, ensuring proper ventilation, securing combustible materials away, maintaining a tidy workspace, and recognizing surroundings to prevent crashes and injuries.
Can I Fix a Weld Without Renovating the Entire Joint?
Repairing a weld without redesigning the entire joint is feasible, relying on the damage (Montana Mobile Welding and Repair Belgrade Welding). Strategies such as grinding, adding filler product, or using a welding process can effectively attend to certain problems while preserving the surrounding framework
What Equipment Are Important for Reliable Welding Fixes?
Vital tools for reliable welding fixings consist of a welding maker, cord brush, grinder, safety equipment, clamps, and filler products. Each device plays a crucial duty in ensuring high quality and safety throughout the repair service process. Porosity typically develops from contamination, dampness, or improper welding methods, which allow gases to escape into the liquified weld pool. Inadequately maintained equipment, including welding machines and tools, may aws d1 4 present variances in the weld grain, more contributing to imbalance. When subjected to the extreme warmth of welding, products typically undergo adjustments that can lead to distortion. Splitting is an usual issue experienced in welding fixings, typically resulting from different variables such as incorrect air conditioning rates, product selection, or insufficient joint preparation. A significant problem in welding fixings is insufficient combination, which happens when the weld steel does not properly bond with the base material or previous weld passes.
Comments on “Common weld defects Montana Mobile Welding and Repair Belgrade Welding helps eliminate”